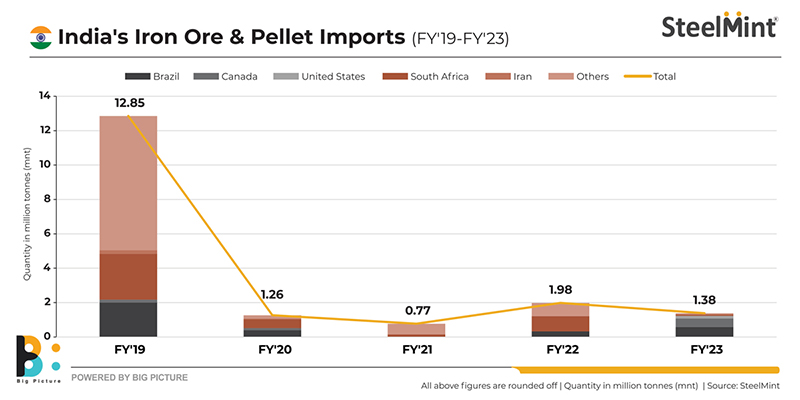
In a recent development, certain Indian steel mills have started importing Australian iron ore fines in place of mainstream Brazilian iron ore concentrates.
SteelMint has heard that Australian miners have started supplying low- to medium-grade iron ore fines (Fe57%-60.5%) to western India-based mills, with recent news of major miner Roy Hill commencing shipments after a pause of five years. An estimated volume of 0.5-1 million tonne (mnt) of shipments have been heard of late. Vessel named “Hedwig Oldendroff” carrying 179,500t Australian iron ore fines is expected to arrive at Jaigad port by end Jun’23.
Preference for fines instead of concentrates can be traced to the fact that mills are most likely increasing the sinter burden in their blast furnaces instead of pellets, SteelMint learn from market sources. This is because it is difficult to ship and transport iron ore concentrates over long distances in the rainy season.
Indian mills typically feed 25-30% of pellets and 50-55% of sinter as charge mix in blast furnace, although this differs across steel mills. Notably, the leading private sector mills, with considerable pelletisation capacities, are increasing the pellet burden in their blast furnaces to maximise gas permeability through charge mix for efficient reduction, higher energy utilisation, and keeping the slag rate per tonne of hot metal under check so as to maximise output and efficiency.
Why are mills turning to imports?
Low global iron ore prices: Indian mills remained favourably inclined towards imports, with iron ore prices falling quickly since the second half of April as expectations of a rapid Chinese recovery faded. Prices of mainstream Australian fines (Fe 62%) dropped below the psychological $100/t CNF China level in the last week of May. Although prices have climbed in the first week of June on China interest rate cuts and stimulus hopes, the low- to medium-grade fines cargoes had been booked by Indian mills when prices had sunk. Also, given the steep freight charges and hassles involved in transporting domestic iron ore from, say, Odisha to the western part of India, mills showed preference for imports.
Quality issues: Domestic iron ore has a higher gangue content compared with imported ore. The level of alumina + silica in domestic ore is markedly higher than Australian material and is obviously better suited for sintering purposes and leads to higher efficiency in the blast furnace.
Logistical bottlenecks: Over and above high domestic freight charges, logistical hurdles such as unavailability of rakes pose a major problem for mills. Logistical difficulties intensify during the monsoon season, which tilts the balance in favour of imports for some coast-based mills.
6th Indian Iron ore & Pellet Summit
India’s iron ore consumption is slated to rise to 360 mnt by 2030, as per SteelMint estimates, in tandem with fast-paced growth in crude steel production. While domestic iron ore capacity expansion has gathered momentum, especially after the transition to the auctions regime, it is believed that imports may increase. This may be due to probable changes in the policy landscape or with depletion of high-grade domestic reserves, with the requirement for higher grades increasing amid the decarbonisation wave sweeping across the industry.
For in-depth insights into these issues and more, register for SteelMint Events’ 6th Indian Iron ore & Pellet Summit to be held at JW Marriott, Kolkata, from 24-26 August, 2023.